Injection blow molding (IBM) is an advanced technology that revolutionizes the production of high-quality plastic bottles. This method offers unique advantages over other manufacturing processes, making it a preferred choice for industries requiring precision and superior finish, such as pharmaceuticals, food and beverage, and personal care products. Having worked closely with multiple manufacturing units, I've accumulated extensive experience that underscores the effectiveness and efficiency of injection blow molding in creating durable and aesthetically appealing bottles.
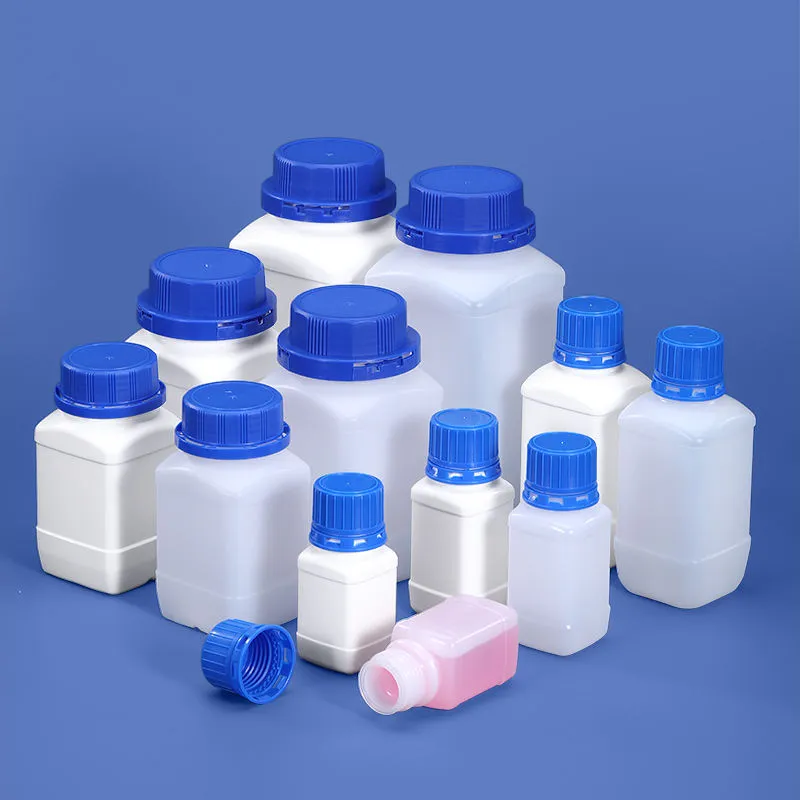
The IBM process begins with an injection phase, where a thermoplastic polymer is heated and injected into a preform mold to create a preform or parison. This initial stage is crucial as it sets the foundation for scalability, strength, and clarity of the final product. The choice of polymer, such as PET, HDPE, or PP, can significantly impact the durability and transparency of the bottles, thereby affecting product presentation and shelf appeal. Expertise in selecting the appropriate material based on end-use requirements can enhance product performance and consumer trust.
Following the injection stage, the parison is transferred to a blow mold where it is inflated into the shape of the desired bottle. This step requires precision, as the mold's design dictates the final product's dimensions and wall thickness. Real-world experience has shown that maintaining consistent wall thickness is vital for ensuring product integrity, especially under variable pressures that packaging might encounter during transportation and handling. Technological advancements, such as computer-aided design (CAD) and finite element analysis (FEA), enable engineers to predict and optimize bottle performance, enhancing the structural resilience of the final product.
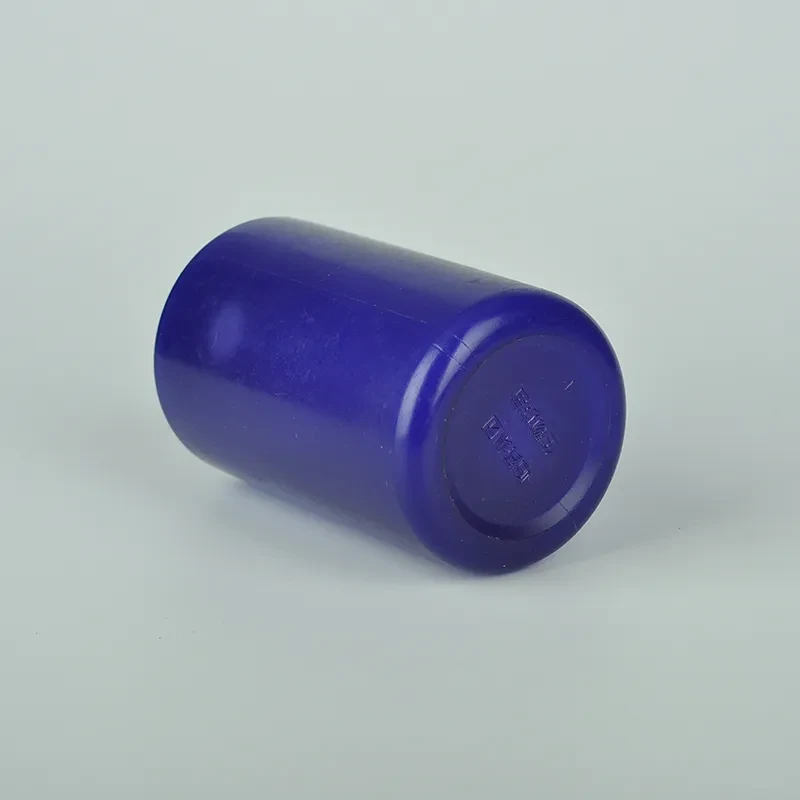
Moreover, injection blow molding allows for seamless integration of features like handles, complex neck structures, or threaded finishes, which are often challenging with other manufacturing techniques. This capability is particularly beneficial for products that require child-resistant closures or specific dispensing needs. The expertise in designing custom molds and the authoritative understanding of mold engineering are indispensable in achieving these intricate features without compromising the production speed or costs.
injection blow molding bottles
Trustworthiness in this process is anchored in the rigorous quality control mechanisms inherent in IBM. The closed-system nature of the procedure reduces the risk of contamination, ensuring the safety and purity of products held within. Each bottle can be subjected to various quality checks, including stress testing, leak detection, and visual inspections, to assure compliance with industry standards and regulations. This level of scrutiny not only validates the reliability of IBM bottles but also reinforces consumer confidence in product safety, a critical factor for brands aiming to uphold a reputable market presence.
Advanced monitoring systems can track production metrics in real-time, enabling swift response to deviations or defects, thereby minimizing production waste and promoting sustainability. Incorporating sustainable practices, such as recycling excess material and implementing energy-efficient machinery, demonstrates a commitment to environmental responsibility, further enhancing the brand’s image among environmentally-conscious consumers.
Throughout this extensive experience with injection blow molding, it is clear that the strategic and judicious use of this technology can yield significant competitive advantages. From unparalleled design flexibility to stringent quality assurance, the expertise embedded in IBM processes empowers manufacturers to deliver products that meet and exceed market expectations. As the demand for precise and reliable packaging solutions grows, leveraging the authoritative knowledge and technological advancements in injection blow molding proves indispensable in maintaining an edge in the ever-evolving market landscape.