When it comes to ensuring that medicine liquid bottles meet the highest standards of quality, safety, and efficacy, a comprehensive understanding of their features, manufacturing processes, and regulatory requirements is essential. These bottles, ubiquitous in households and essential in medical facilities, play a critical role in the accurate dispensation of liquid medications.
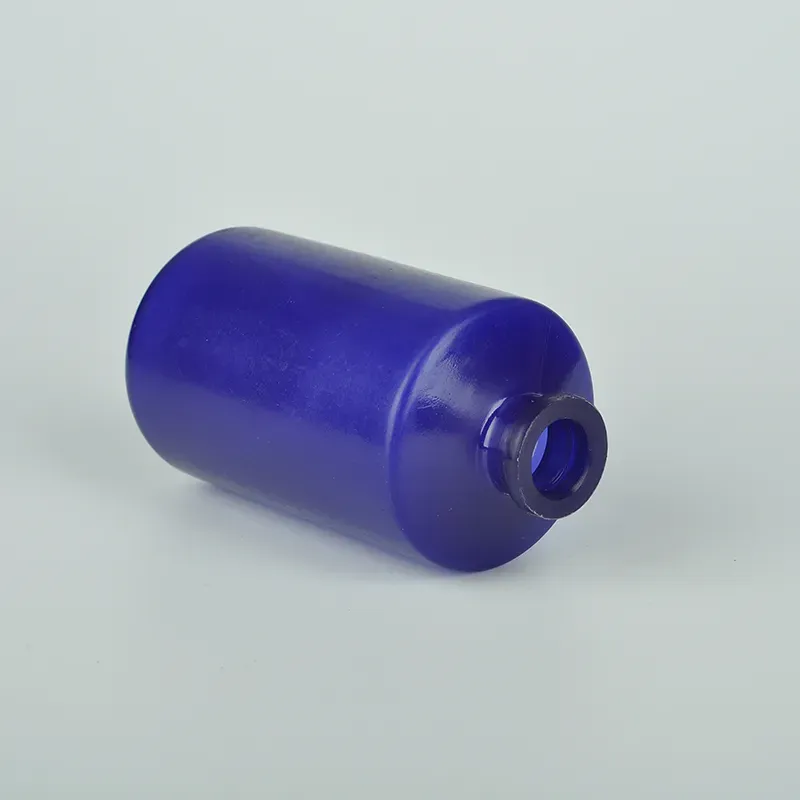
At the heart of the design of a medicine liquid bottle is the need for precision and safety. Such bottles are typically crafted from high-grade plastics or glass to prevent any chemical interaction with the medicine inside, ensuring that the efficacy of the medication remains uncompromised. A precise volumetric indicator is often printed on the bottles, enabling patients and healthcare providers to dispense exact dosages, thereby avoiding underdosing or overdosing, which can lead to ineffective treatment or adverse reactions, respectively.
The manufacturing process of these bottles is where expertise truly comes into play. Advanced engineering and technological solutions are deployed to ensure that each bottle maintains uniformity in terms of its structural integrity and capacity. Quality control is a critical component of this process; each batch of bottles undergoes stringent testing for any defects, including leakage and material weakness. This attention to detail not only guarantees that every bottle can hold and protect its contents effectively but also reinforces the trustworthiness of the products that reach the market.
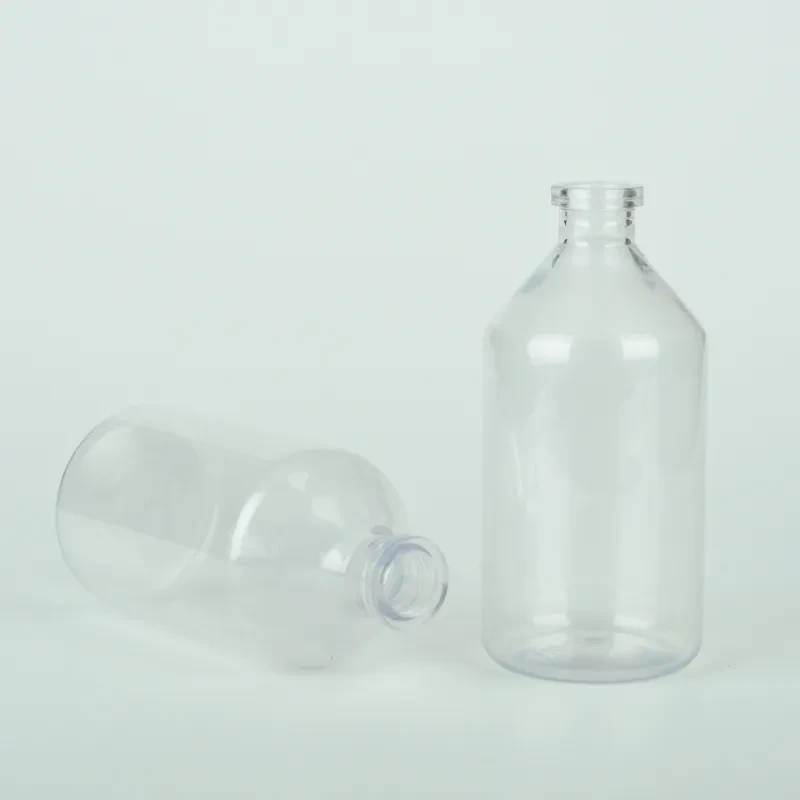
In terms of regulatory requirements, medicine liquid bottles must adhere to strict international standards to be deemed safe for use.
Regulatory bodies such as the U.S. Food and Drug Administration (FDA) and the European Medicines Agency (EMA) have outlined comprehensive guidelines that manufacturers must follow. These include specifications for material composition, container closure integrity, and labeling accuracy. Compliance with these regulations is not just a legal obligation but also a testament to the manufacturer's commitment to delivering quality products.
medicine liquid bottle
Another layer of trustworthiness is added through innovations in child-resistant packaging. Often, the caps of medicine liquid bottles are designed to be childproof, requiring a sequence of actions to open. This safety feature is paramount in preventing accidental ingestion by children, a common household hazard.
From an experiential standpoint, user feedback is invaluable in refining the design and usability of these bottles. Patients and caregivers often cite ease of use, legibility of dosage markings, and cap security as crucial factors in their overall satisfaction with the product. Manufacturers regularly incorporate this feedback into design improvements, ensuring that the bottles are both user-friendly and effective.
Furthermore, with the global shift towards sustainability, there is a growing demand for environmentally-friendly materials in the production of medicine liquid bottles. Innovations in biodegradable plastics and recyclable materials are steadily becoming the norm, driven by both regulatory pressures and consumer preference for greener products.
In conclusion, medicine liquid bottles are much more than simple containers; they are complex products that embody a synthesis of expertise, regulatory compliance, user experience, and technological advancement. For stakeholders in the healthcare industry, understanding these aspects is fundamental to ensuring that they are providing safe, effective, and reliable medication solutions to their patients. Through continued innovation and adherence to the highest standards, manufacturers of medicine liquid bottles can ensure that they remain authoritative and trusted players in the healthcare sector.