Plastic drug vials have revolutionized the way pharmaceuticals are packaged and dispensed, meeting modern healthcare's demand for safety, durability, and convenience. As the pharmaceutical industry continually evolves, the innovation and technological advancements incorporated into plastic vials play a crucial role in defining their utility and efficiency.
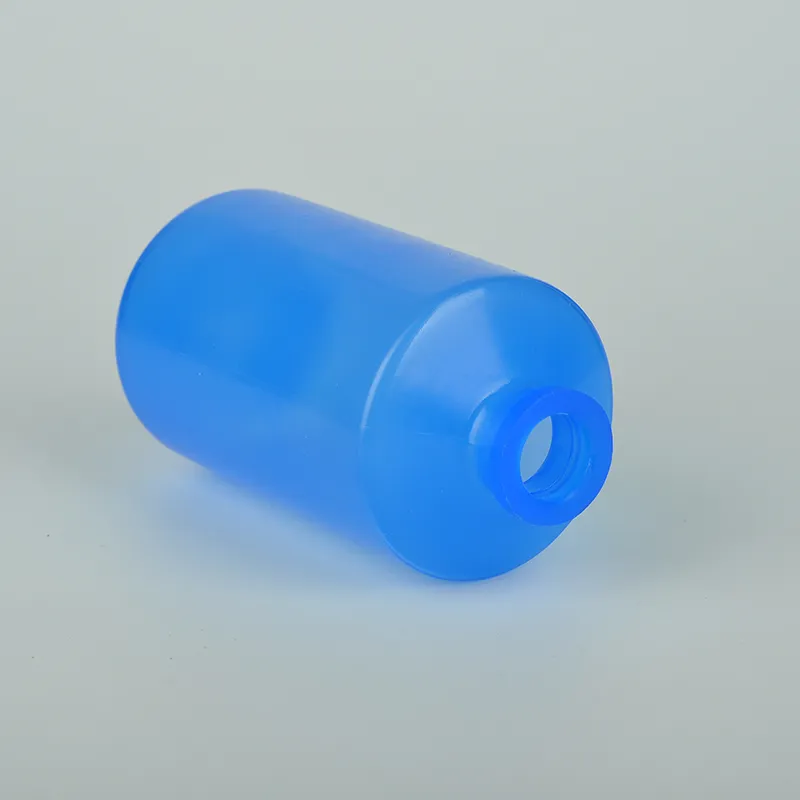
Experience in the field reveals that plastic drug vials are not just containers; they are key allies in maintaining the efficacy and integrity of medications. Their lightweight nature provides ease of transport, enabling them to be a preferred choice for both healthcare providers and patients. The flexibility and resilience of plastic materials offer a robust solution against breakage—a significant advantage over traditional glass vials, especially in fast-paced or resource-variable environments such as hospitals and rural health centers.
Understanding the expertise behind these products involves delving into the specifics of materials science.
The composition of plastic vials is carefully curated to meet stringent medical standards. High-density polyethylene (HDPE) and polypropylene are common materials used due to their impermeability and resistance to chemical interactions, which ensure that the contained drug remains untainted by external factors. Their production involves precision engineering where cleanliness and sterility are prioritized to prevent contamination, thus adhering to Good Manufacturing Practices (GMP).
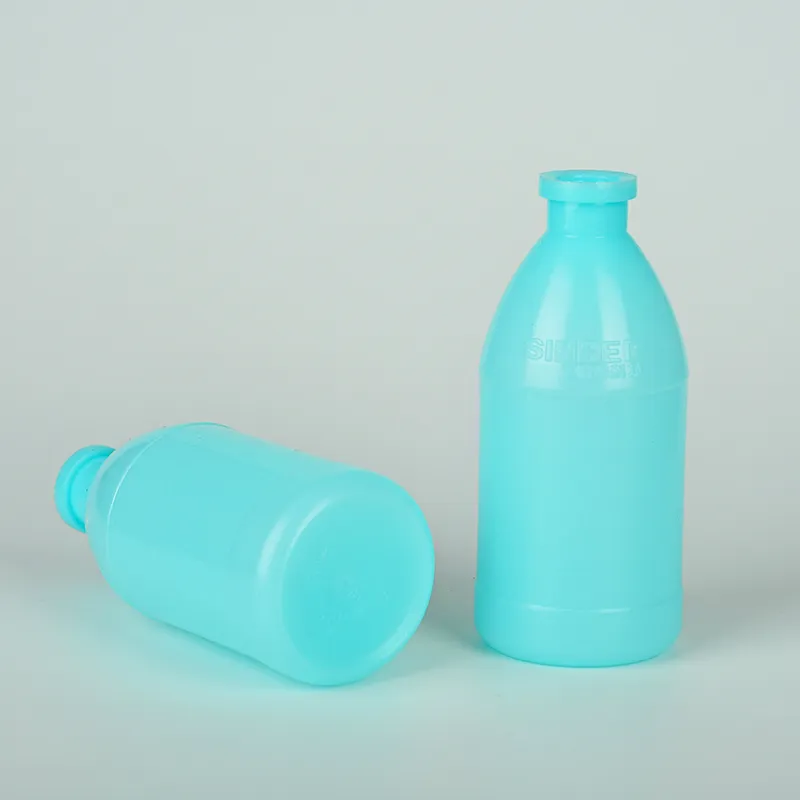
The design of plastic drug vials also reflects a deep expertise in user-centric innovations. Child-resistant caps are a prime example, combining safety with accessibility to prevent accidental ingestions by children while still being elder-friendly. The advancements in tamper-evident features further underline a commitment to safety, reassuring consumers of the product's untouched nature since leaving the factory.
plastic drug vials
Authoritativeness in the production and use of plastic vials is exemplified by adherence to regulation and compliance benchmarks set by international health organizations, such as the FDA and WHO. These vials undergo rigorous testing protocols to verify their compatibility with different pharmaceutical compounds and ensure they meet all safety guidelines. Manufacturers often employ a team of experts, from chemical engineers to pharmacologists, to continuously improve these products, as well as to ensure they meet evolving safety standards.
Trustworthiness of plastic drug vials is built over years of reliable performance. Healthcare providers rely on their proven track record for consistent quality, which is achieved through precision control during manufacturing processes. Serialization and barcode integration on labeling are implemented for better traceability and inventory management, assisting pharmacists in maintaining accurate dispensing records.
Patient testimonials often emphasize the convenience that plastic drug vials bring into their daily medication regimen. Their transparent nature allows for quick visual assessment of the contents, while the ergonomic designs ensure easy handling. Moreover, the recyclability of many plastic vials aligns with the increasing consumer demand for sustainable healthcare solutions, contributing positively to environmental stewardship initiatives.
In conclusion, plastic drug vials exemplify a harmonious blend of experience-driven insights, specialized expertise, authoritative manufacturing practices, and an overarching trustworthiness. They represent an indispensable innovation within the pharmaceutical supply chain, enhancing medication safety and efficacy while providing a user-friendly packaging solution. As the industry continues to innovate, plastic drug vials will undoubtedly remain a cornerstone of modern pharmaceutical packaging, promoting better health outcomes worldwide.