In the realm of modern pharmaceuticals, plastic drug vials play an indispensable role in the packaging and delivery of medications. From the perspective of experience, these vials are designed to meet the rigorous standards necessary for the safe transport and storage of drugs. Crafted with precision, they protect against contamination and degradation, ensuring that the medication maintains its efficacy over time. For patients and healthcare providers alike, the integrity of these vials translates directly into trust in the medication itself.
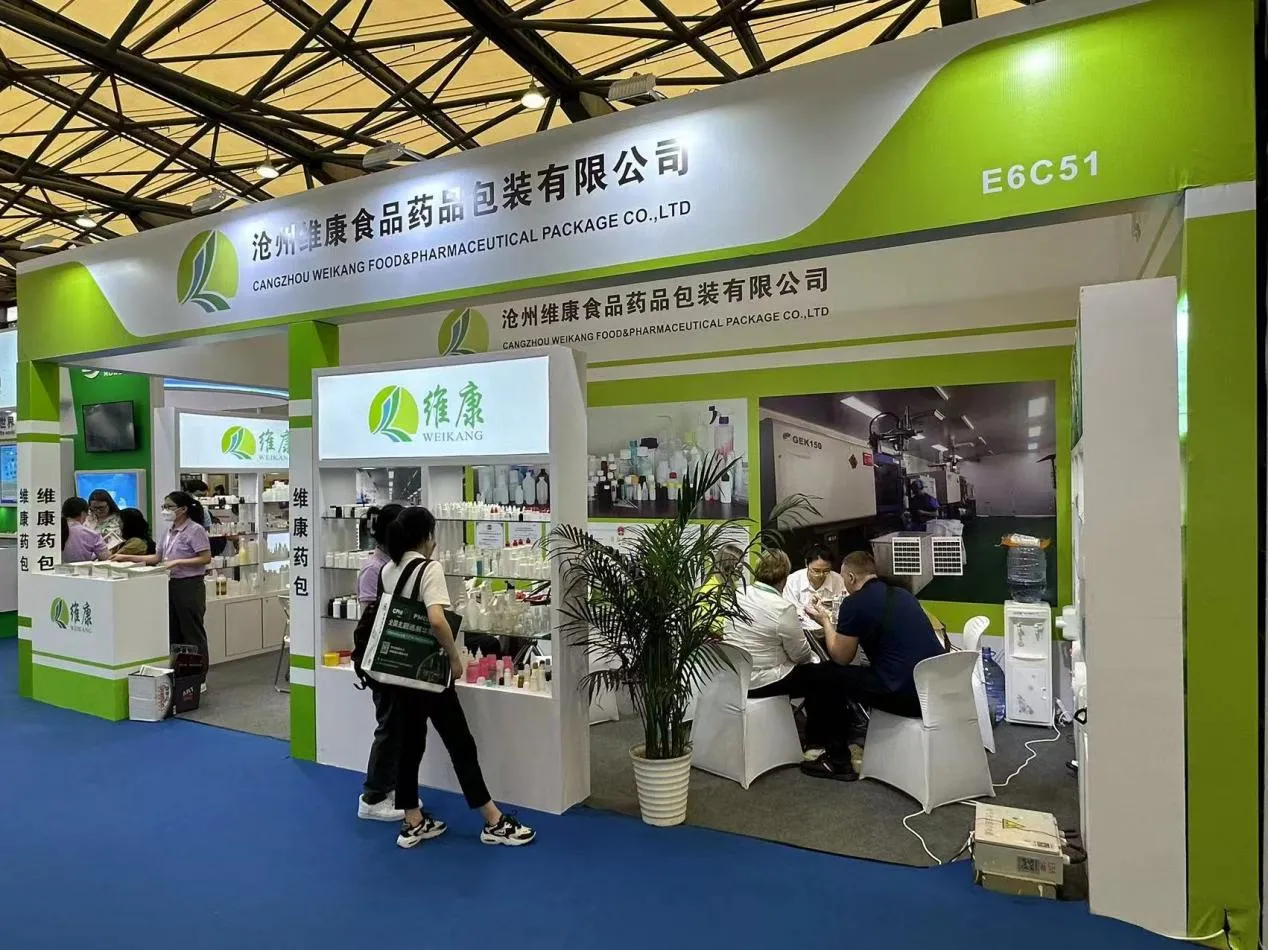
Moreover, the expertise involved in manufacturing plastic drug vials is a testament to the advances in pharmaceutical packaging technology. These vials are manufactured using medical-grade plastics, often featuring materials such as Polyethylene (PE) or Polypropylene (PP), which offer a balance of durability and medical safety. The choice of material is crucial as it provides resistance to various chemicals and temperature changes, while remaining lightweight and cost-effective for large-scale distribution.
From an authoritative standpoint, plastic drug vials must adhere to stringent regulatory standards. Organizations like the FDA in the United States and the EMA in Europe provide the regulatory framework that ensures these vials meet necessary safety and efficacy requirements. Manufacturers often undergo exhaustive testing processes to certify that their products are not only compliant with these standards but also superior in terms of usability and patient safety. These rigorous tests examine factors such as the vial's barrier properties, chemical compatibility, and closure integrity.
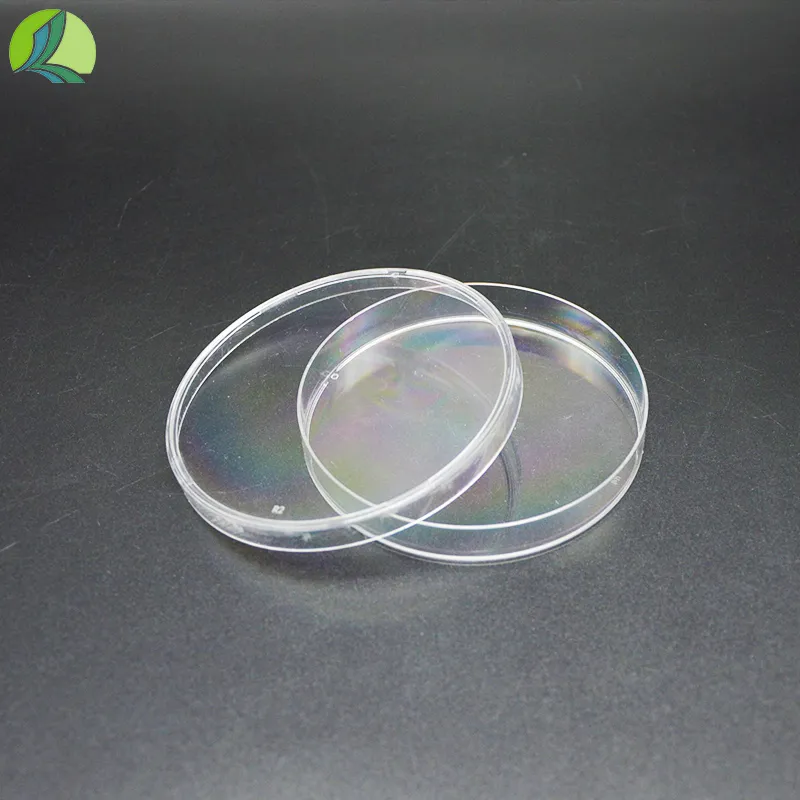
The trustworthiness of a plastic drug vial is further established through its tamper-evident features. With enhancements in cap design and security sealing, these vials provide clear evidence if any unauthorized access has occurred. This layer of security is critical in maintaining patient trust, as it reassures users that the medication has not been compromised from the moment it leaves the manufacturer to the point of administration.
plastic drug vials
Exploring the product space, many manufacturers now offer highly customizable options for plastic drug vials. This customization can include color-coding to differentiate drug types, child-resistant caps for safety, and even smart labeling technology which integrates with digital systems to offer real-time data tracking. Such innovations not only enhance the user experience but also ensure compliance with medication regimes, ultimately improving health outcomes.
Plastic drug vials are favored for their adaptability. They are designed to accommodate a wide range of substances, from solids like tablets to liquids like injectable solutions, which require precision-engineered closures to prevent leaks and exposure. Their versatility is further underscored by the availability of various sizes, designed to cater to specific dosages and treatment durations. This aspect of scalability is crucial as it aligns with the diverse needs of pharmaceutical companies that produce a wide array of medicinal products.
Environmental considerations have also become increasingly important in the production and disposal of plastic drug vials. Leading manufacturers are investing in developing biodegradable materials and advocating for robust recycling programs. These efforts reflect a commitment to sustainability, which is becoming a significant purchasing decision factor for healthcare institutions and patients alike.
In conclusion, the ultimate efficacy of plastic drug vials lies in their consistent delivery of reliable, safe, and user-friendly packaging solutions. Engineers and scientists continue to innovate in this space, ensuring that these vials not only meet today’s standards but are also well-equipped to handle the demands of future pharmaceutical advancements. Through ongoing developments and a commitment to quality, plastic drug vials will continue to be a cornerstone of effective drug delivery systems worldwide.